
Tanya Hanway and Ernest Sanchez explain that Leidos’ name comes from the word “kaleidoscope” to represent the company’s ability to solve difficult problems by applying different perspectives, unlocking new insights, and making new discoveries.
A Kaleidoscope of Space Supplies and Innovation to the ISS and Beyond
From a 55,000 Sq Ft facility on Forge River Road in Webster, Leidos supports human spaceflight and deep space exploration to enable NASA’s next great discovery. Leidos’ local team of innovators works on numerous NASA programs spanning mission operations, research and engineering, payload processing, food development, human spaceflight, and IT support. Just about everything astronauts aboard the International Space Station touch, wear, consume, and do bears Leidos’ signature. From laptops to space suits, tortillas, toothpaste, and experiments, Leidos has shipped more than 210,000 pounds of supplies to the International Space Station.
In Webster, Leidos’ focus is enabling NASA’s mission of driving innovation in science, technology, aeronautics, and space exploration. The 129-member team inside the Forge River Road facility and 284-member team on site at Johnson Space Center prepare astronauts for space travel, zero-gravity living, and daily work aboard the largest spacecraft ever built—the International Space Station (ISS)—which circles the earth at 17,000 mph and is the astronauts’ habitat for an average of six-month intervals.
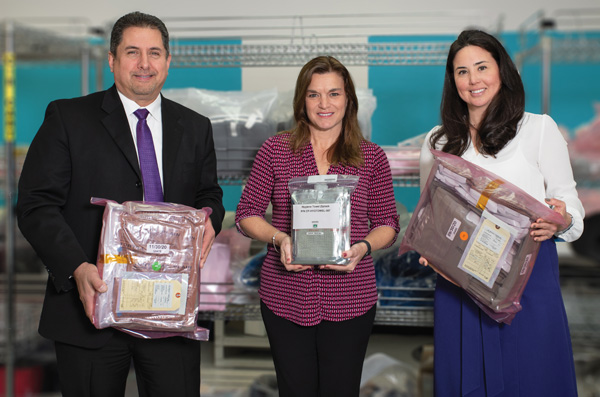
Inside Leidos’ Cargo Processing Facility, Cargo Mission Contract Program Manager Ernest Sanchez; Division Manager of NASA Programs Nan Hardin; and Research, Engineering, Mission Integration Services Program Manager Tanya Hanway hold kits of essential supplies, like food and hygiene towels, bound for the ISS. Prior to transport, cargo undergoes about 200 different processes inside the Webster facility.
Special Delivery to the ISS and Beyond
Leidos’ development of clothing, gear, food, and equipment for those aboard the ISS holds significant ramifications for space colonies on the moon, Mars, and beyond. Logistics falls into this category, as well. Just as astronauts on the ISS require regular deliveries of experiment equipment, spare parts, food, air, and water, those who inhabit space outposts will need resupplies, too. Leidos’ expertise in planning, processing, and packing more than 400,000 pounds of supplies annually to the ISS is of critical importance—especially when every ounce matters. Leidos inventories, labels, and fit-checks each piece of hardware and soft goods, like a puzzle, to fit within a cargo transfer bag. Leidos’ very name, which appears in the word “kaleidoscope” to convey a constantly changing shape and form, represents the company’s innovative mindset toward solving problems and making new discoveries. Leidos’ prowess in technology and its far-reaching science and research applications play a vital role in human space activity.
kaLEIDOScope Leidos Innovates
Under NASA’s Cargo Mission Contract (CMC) in the Webster facility, Leidos processes cargo to enable astronauts’ daily health, welfare, and work aboard the ISS. The sheer number of steps and scope of work involved in making, assembling, processing, inventorying, labeling, testing, imaging, certifying, and integrating everything that is sent to ISS crewmembers is mind-boggling. Shipments often include crew provisions, hand tools, equipment, cameras, batteries and power supplies, research experiments, and ISS hardware.
Space-rated Yeti™
The majority of the thousands of different experiments and critical systems hardware that are bound for space are developed at various facilities and sent to Leidos’ Webster team for packaging and packing for launch to orbit. However, Leidos also plays a critical role in fabricating and developing products for use in space. For example, when NASA wanted to research a low cost, low risk alternative for passively transporting frozen items to the ISS, Leidos’ engineers were charged with developing a custom Passive Cold Stowage Box (PCSB) that could maintain subzero temperatures for up to a week without battery or vehicle power. Essentially, NASA asked if Leidos could develop and certify a space-rated Yeti®, and within months, the ISS crew was surprised with a shipment of frozen fruit bars to the ISS to enjoy as proof of concept. Leidos has developed many useful and innovative solutions, including a reliable power supply for laptops, a larger, safer, and more efficient food warmer, and a multi-layer insulation blanket needed to protect cargo from extreme temperatures that is fully compatible with the ISS robotic arm.
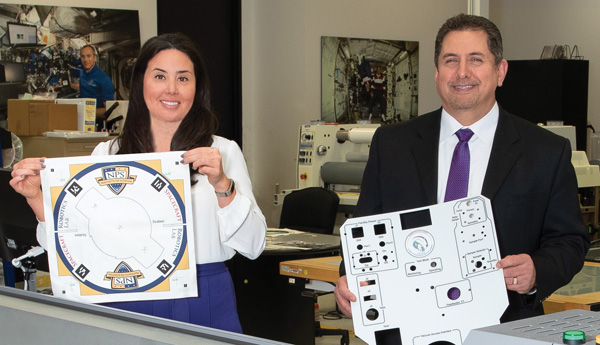
Inside the Decal Lab, 8,000 to 10,000 decals are created each month to support ISS missions. Decals, labels, and placards are generated for everything—contents, barcodes, tracking info, serial numbers, operating instructions, and safety.
Shipments to ISS average between 4,000 and 7,700 pounds
Inside Leidos’ Webster CMC facility, packaging takes on a completely new meaning. Bubble bags, Ziplocs, and Velcro abound inside the main cargo processing room, as well as the ubiquitous cargo transfer bags that come in various sizes to hold just about everything. Special shipping containers and lifts to handle heavy equipment are complemented by imaging services, HAZMAT assessments, and Department of Transportation coordination. Cargo kits become part of cargo transfer bags, which are clearly labeled and contain stringent inventory data to ensure that all hardware is handled in accordance with safety protocols. Electronic Launch Return On-Orbit Data Sets (eLRODS) protect hardware during all phases of processing—from receipt, ground handling, and delivery to the ISS. Custom foam enclosures made in the Foam Operations Lab protect flight hardware, just as decals, labels, and placards created in the Decal Lab protect and aid astronauts, so they know the precise sequencing for unpacking, setup, and operations. Labels are created in accordance with stringent NASA flight-approved materials and certifications and contain essential safety, inventory, tracking, and operating information.
Leidos’ work is not all inventorying, packaging, and labeling. The Webster team also works to ensure astronauts are healthy and comfortable. In fact, Leidos touts a seamstress who tailors clothing for astronauts and fabricates specialty items and equipment. Buttons on shorts or pants must be replaced with Velcro closures, and pockets with straps or closures must be added. Special equipment and soft goods are also fabricated inside the Webster facility. For instance, Leidos designed a camera covering that allows an astronaut’s huge, thick glove to handle and actuate buttons on the camera during a spacewalk or extra vehicular activity (EVA).
Leidos also considers toiletries and astronaut hygiene in its cargo preparation. Every kilogram counts for payloads; water must be imported to the ISS, as no method for cleaning clothes currently exists. This means astronauts receive a single clothing kit, clearly labeled for two weeks’ worth of wear. A change of outfit might transpire twice a week. Astronauts can choose among their favorite brands for hygiene products, such as shampoo, toothpaste and deodorant—many of which will be outfitted with a Velcro backing.
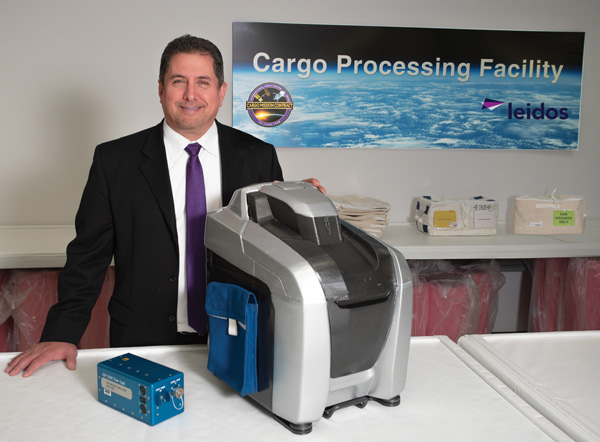
Ernest Sanchez displays a 3D printed mock-up of the Keyence BZ-X800E All-In-One Fluorescence Microscope, an automated microscope with high-resolution imaging and analysis system, that was recently certified by Leidos for use on the ISS.
Manifest to Delivery: Six Weeks 13-15 Flights to ISS Annually
While food is made off-site, all of it is labeled, packaged, and processed in Webster where it’s categorized, numbered, placed into kits, and pressurized for transport. Factors, like nutrition, digestion, dietary conditions, shelf life, and zero-gravity have a huge role in determining what astronauts eat. A four-pound bag labeled “fruits and nuts,” for example, contains individual bags of almonds, apples with spice, applesauce, berry medley, cashews, dried apricots, dried pears, fruit cocktail, macadamia nuts, peaches, peanut butter, peanuts, and more—clearly listed in alphabetical order with tracking or inventory number.
Just as Leidos processes nearly all of the cargo that goes to the ISS, the Webster facility is the repository for returning payloads, as well. This includes time-sensitive or temperature-critical experiments, research materials, malfunctioning hardware, and used, but valuable, gear and equipment. The constant challenge to innovate and develop new modes for life and work in space is Leidos’ focus in Webster and at Johnson Space Center.
Next Stop: Lunar Station
Leidos is poised now to be the supplier to Gateway—the lunar orbital platform that brings astronauts to the moon to operate a space station and serves as a “gateway” for deep space missions. Under the Research, Engineering, Mission Integration Services (REMIS) contract, Leidos is currently developing the navigation and alignment aides for the Gateway Program to ensure safe docking of the various modules. Additionally, as commercialization of low earth orbit continues to ramp up rapidly, Leidos’ unparalleled expertise in logistics, research, engineering, IT, and mission integration services is in demand.
With a track record of success at NASA centers across the country, Leidos provides the mission understanding and technical expertise necessary to support advancements in space exploration and human spaceflight across the public and private space sector. From enterprise IT modernization to operations and logistics to systems engineering and integration, Leidos stands ready to support NASA in achieving its next discovery.